Ultra precision grinding with diamond micro powder grinding wheel, existing technical problems and development prospect. The ultra precision grinding mechanism of diamond micro powder grinding wheel is discussed. It is considered that it is the fusion of multiple functions dominated by micro cutting; The dressing mechanism of diamond micro powder grinding wheel and its common effective dressing methods are studied; The conception of resin metal composite bonded diamond micro powder grinding wheel is put forward, and its structure formation, manufacturing process and actual grinding effect are discussed. Finally, the influencing factors and environmental conditions of ultra precision grinding with diamond micro powder grinding wheel are discussed.
1. Foreword
Ultra precision cutting with diamond tools has achieved great success in processing soft metal materials such as copper, aluminum and their alloys. However, in the precision and ultra precision processing of hard and brittle materials such as engineering ceramics, semiconductors, optical glass and stone, it still depends on grinding, polishing and other processing methods to a great extent, Although these methods can achieve high precision and very low surface roughness, the machining efficiency is low, and it is difficult for ultra precision machining of some complex shapes, such as aspheric parts.
Grinding hard and brittle materials with diamond grinding wheel is an effective super hard abrasive precision machining method. It has strong grinding ability, good wear resistance, long service life, small grinding force, low grinding temperature, no burn, crack and microstructure change on the surface, good machining surface quality and high grinding efficiency. Therefore, it has been widely used in recent years, However, it is difficult to meet the higher requirements of ultra precision machining in geometric accuracy and surface roughness. Therefore, an ultra precision grinding method with diamond micro powder grinding wheel is proposed.
According to China’s national standards, the diameter of abrasive particles is 50 μ M is hereinafter referred to as micro powder. Diamond micro powder grinding wheel is generally sintered with diamond micro powder with particle size of w40-w5 as abrasive and resin, ceramic and metal (such as copper, fiber cast iron, etc.) as binder. Its characteristics are as follows:
(1) Diamond micro powder grinding wheel can obtain very low surface roughness because of its fine particle size. At the same time, high grinding precision can be obtained by grinding on precision grinder or ultra precision grinder. It is an ideal micro nano ultra precision machining method.
(2) Ultra precision grinding with diamond micro powder grinding wheel is a micro removal method of consolidated abrasive. It has the characteristics of general grinding. It can easily grind the surface of outer circle, hole, plane and forming. It has high machining efficiency and good machining quality, and has great development prospects.
(3) Because the abrasive particle size of diamond micro powder grinding wheel is very fine, the chip holding space is very small, and the debris is easy to be blocked, in addition to general dressing, on-line dressing is also needed to ensure the normal grinding and machining quality. Originally, the dressing of superhard abrasive wheel is a difficult problem. Therefore, the dressing of diamond micro powder wheel is a key technology.
(4) Because the chip holding space of diamond micro powder grinding wheel is very small, the grinding depth during grinding should be strictly controlled. The grinding should be carried out on precision grinding machine or ultra precision grinding machine, and the machine tool should have micro feed system.
2. Ultra precision grinding mechanism of diamond micro powder grinding wheel
The traditional precision machining and ultra precision machining methods with free abrasive, such as grinding and polishing, are mainly based on the plastic deformation and plastic flow of the machined surface caused by the rolling and extrusion of abrasive particles, as well as the micro cutting of abrasive particles, which can be summarized as extended grinding.
In ultra precision grinding with diamond micro powder grinding wheel, it is mainly micro cutting. In the cutting process, there are phenomena such as chip formation, plough (uplift), sliding friction (sliding and friction), which is due to the large negative rake angle and blunt radius of cutting edge; Because it is a micro powder abrasive particle, it has micro edge; At the same time, due to the fine dressing of the grinding wheel, the abrasive particles have good contour on the surface of the grinding wheel, so the cutting mechanism is relatively complex. The following phenomena can be analyzed:
(1) The chips form relatively high (prominent) and sharp abrasive particles distributed on the surface of the grinding wheel, which can obtain a large enough grinding depth, form chips, and see the sparks generated by oxidation and combustion when the chips leave the workpiece surface.
(2) Plough is distributed on the surface of grinding wheel, and the abrasive particles that are not prominent and sharp enough can not form chips. Only furrows can be drawn on the surface of workpiece, and bulges can be formed on both sides of furrows, which will affect the surface roughness.
(3) Sliding friction some abrasive particles distributed on the surface of the grinding wheel have low protrusion height and sharpness, can not form chips and plough, and can only produce sliding and friction on the workpiece surface. Due to the high grinding speed, grinding heat will be generated, resulting in thermoplastic flow and affecting the surface quality.
(4) Extrusion and plastic deformation some abrasive particles distributed on the grinding wheel have very small projection height and no edge. They can only squeeze the contour peak of the machined surface to produce plastic deformation and tend to be flat and smooth, so as to improve the surface roughness.
(5) Elastic failure in crystal structure materials, there are lattice defects, generally about 1 Lin. There is a dislocation defect within the interval. During ultra precision grinding with diamond micro powder grinding wheel, the action range of machining stress is that the average l of dislocation defects can be separated (1 Lin m), so it will produce atomic or molecular elastic failure. This failure will not produce plastic deformation and residual metamorphic layer, but has an impact on the surface microstructure.
3. Dressing of superhard abrasive wheel
At present, superhard abrasive refers to diamond and cubic boron nitride. The dressing of superhard abrasive wheel has always been a difficult problem.
2.1 dressing process of superhard abrasive wheel
The dressing of superhard abrasive wheel is generally divided into two processes: shaping and dressing.
Reshaping is to make the grinding wheel reach a certain size and geometry. It is usually carried out when the grinding wheel products leave the factory. However, when the grinding wheel is used, due to the installation error installed on the grinder spindle, such as the outer circle of the grinding wheel is not concentric with the grinder spindle or its end face is not perpendicular to the grinder spindle, it must be reshaped. In addition, shaping is also required for forming grinding. Shaping requires a certain precision of size and geometry, and has high efficiency.
Dressing is mainly to make diamond abrasive particles protrude to form cutting edge and chip holding space for grinding. Because diamond is very hard and difficult to be processed by other materials, dressing is mainly to remove the bond around diamond abrasive particles and expose them. If too much is removed, diamond abrasive particles may fall off, If the removal is too little, the cutting edge and sufficient chip holding space may not be formed, and it is usually appropriate to expose one third. During the sharpening process, some diamond abrasive particles may break and form new edges, which is related to the sharpening method used.
In the dressing of ordinary grinding wheel, the shaping and sharpening are usually completed in one step. During the dressing, the abrasive particles are mainly broken to form new edges, so the dressing mechanism is different.
2.2 dressing method of superhard abrasive wheel
There are many dressing methods for superhard abrasive grinding wheel. Here are several effective common dressing methods:
(1) The grinding method of silicon carbide (g) c cup wheel is shown in Figure 1. The dresser is installed on the grinding machine workbench. During trimming, the axis of the cup wheel is perpendicular to the axis of the trimmed wheel, and the cup wheel is along the tangent of the circumference of the trimmed wheel
In each reciprocating motion, when the cup-shaped grinding wheel is separated from the trimmed grinding wheel, a certain amount of cutting is carried out in the vertical direction. This dressing method is more practical, but the cup-shaped grinding wheel has a large loss. Its dressing mechanism is to remove the bond around the diamond abrasive particles by the falling abrasive particles of the silicon carbide cup-shaped grinding wheel during dressing. The dressing method of cup-shaped grinding wheel was proposed by Professor Chuang sik Hsiung of Tohoku University in Japan.
(2) Electrolytic dressing method is shown in Figure 2. The grinding wheel is connected to the positive electrode and electrolyte is connected between it and the negative electrode. When energized, the current is transmitted to the grinding wheel by the support through the brush, resulting in electrolysis. The metal bond on the grinding wheel is removed by electrochemical corrosion to achieve the sharpening effect. This method has the advantages of on-line sharpening, simple device and good sharpening quality. It is widely used, but it can only sharpen metal bonded diamond grinding wheels, and special anti-corrosion electrolyte is required to avoid rusting the machine tool. Electrolytic dressing method is proposed by Professor Masahiro Ohmori of Japan Institute of physical chemistry. It is called electrolytic on-line dressing, which is abbreviated as EHD (ELECTROLYTIE in proeess dressing).
(3) The electric spark dressing method is shown in Figure 3. The power supply provides direct current, the grinding wheel is connected to the positive pole, and the dresser is connected to the negative pole to form positive machining. Because the grinding wheel is rotating, the power supply should be connected to the grinding wheel shaft through the brush and then transmitted to the grinding wheel. This dressing method can not only reshape, but also sharpen, and can be used for on-line dressing. The working fluid can be directly used with the grinding fluid of the grinder. The method is simple and convenient and widely used, but it is only suitable for metal bonded grinding wheels. The Institute of manufacturing engineering of Tsinghua University has done a lot of work in this field, which is a promising dressing method of diamond micro powder grinding wheel.
(4) The abrasive belt grinding method is shown in Figure 4. The diamond micro powder grinding wheel is trimmed with corundum and silicon carbide abrasive belt. It is a soft elastic dressing method, which is referred to as elastic dressing method for short, by using the elasticity of the soft material based on the abrasive belt to remove the bonding agent around the diamond abrasive particles. This method can be used for diamond grinding wheels with various binders, and the dressing effect is good, but the shaping aging rate is low, and it is better for dressing. The Institute of manufacturing engineering of Tsinghua University has also done a lot of work in this regard.
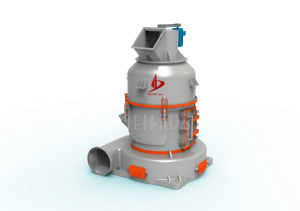