Impact crusher uses impact to crush materials. It has large crushing ratio and high crushing efficiency. Therefore, it is widely used in metallurgy, building materials, light industry, chemical industry, electric power and other industrial departments. There are many parameters of impact crusher, and the variables are interrelated and restrict each other, which jointly affect the performance of the machine. Therefore, mastering these laws, optimizing parameters and structure, and giving full play to its characteristics and functions are of great significance to improve the production efficiency and product quality of the equipment.
1 rotor diameter and length
The rotor diameter of impact crusher is generally related to the size of feed block. When materials are broken, enough impact energy is required. That is, a certain size of rotor diameter is required. The rotor diameter is too small and the impact energy is not enough to break the material; If the rotor diameter is too large, the energy consumption is large, which is unfavorable to energy conservation.
The relationship between rotor diameter and block particle size can be determined according to the following empirical formula:
D = (2 ~ 4) d, where D is the diameter of rotor, mm; D is the maximum feed block size, mm.
Larger value shall be taken for small crusher; The smaller value shall be taken for large crusher.
The rotor length is mainly determined according to the production capacity of the crusher. The ratio of rotor length L to diameter D is generally 0.5 ~ 1.2. When the L / D value is small, the stability of the body structure is poor. This machine can only be used for materials with low hardness. Single rotor impact crusher with low processing capacity, but if the L / D value is too large, the rigidity of the body will become worse.
2 number of plate hammers
The more the number of plate hammers, the more the number of blows per revolution of the rotor, and the better the crushing effect, but too much will make the manufacturing complex and consume more materials. Generally, the number of plate hammers is determined according to the diameter of the rotor.
When the rotor diameter is small, the number of plate hammers is small. Generally, when the rotor diameter is less than 1m, three plate hammers can be installed; When the rotor diameter is 1m ~ 1.5m, 4 ~ 6 plate hammers can be installed; When the rotor diameter is 1.5m ~ 2m. 6 ~ 10 plate hammers can be installed. When the material is hard and the crushing ratio is large, the number of plate hammers can be more.
3 feed guide inclination
The materials of the impact crusher enter the crushing chamber along the guide plate, so the inclination of the guide plate β Is an important parameter. β The smaller the angle, the slower the material slides along the guide plate, and the material can be fully broken to obtain good product quality.
But inclination β Too small will affect productivity and even cause stacking; The greater the inclination angle, the faster the material slides along the guide plate, which is beneficial to improve the crushing efficiency, but too large materials can not be fully crushed, affecting the product quality. In addition, if the inclination angle is large, the height of the crusher should be increased. The dip angle is generally between 45 ° and 60 °. If other conditions permit, it is appropriate to take the smaller value of the dip angle.
When selecting the inclination angle of the guide plate, the relationship between the material sliding out of the guide plate and the plate hammer should also be considered. If the material slides out of the guide plate (leaving the unloading point) and the plate hammer has not arrived in the future (plate hammer lag phenomenon), and the material has not slipped out of the guide plate but the plate hammer is just in place and does not meet the material (plate hammer lead phenomenon), the crushing effect is not good. It is better that the material slides out of the guide plate and meets the plate hammer at the same time. At this time, the crushing effect is the best.
4 guide plate unloading point
The position of the guide plate unloading point is described by the included angle a between the connecting line of the rotor center at the guide plate unloading point and the horizontal line passing through the rotor center. The angle a is small and the height of the crusher is relatively low, which can reduce the height and weight of the crusher. It is very beneficial to reduce the height of the mobile crusher.
In addition, the small a angle can also increase the arc length of the crushing chamber. But a is too small and the counterattack is not strong enough. The particle size of the material can not meet the process requirements, and the material is too large, which is easy to cause material blockage in the body. Therefore, the value of a should be reasonably determined. If other conditions permit, a should be smaller. Generally, a ≤ 30 ° is more appropriate.
5 hanging position of reaction plate
There are many parameters of the hanging position of the impact plate, and they have the greatest impact on the performance of the crusher (taking the hanging position of the first stage impact plate of the second stage impact plate as an example).
The suspension position parameters of the first stage reaction plate include x, y δ、θ And △. As shown in the figure.
Structural dimensions of impact crusher
x. Y is the position of the starting point of the first stage first section impact plate. x. Y is too large, the running distance of materials is long, the speed and momentum of materials impacting the plate surface decrease due to resistance, and the crushing effect is not good; x. Y is too small. The acceleration time of materials is short, and they impact the plate surface before reaching the maximum speed and momentum, which is not conducive to crushing.
Therefore, according to the crusher rotor diameter D and the inclination angle of the feed guide plate β、 Strike angle α Choose mushrooms X and Y reasonably. Generally, x = (0.15-0.35) d, y = (0.70 ~ 1.20) d. α、β If the value is large, the relatively large value shall be taken; α、β If the value is small, take the relatively small value; If the crushing particle size is large and the hardness is large, the larger value shall be taken.
δ It is the included angle between the tangent of the outer circle of the plate hammer and the vertical line of the impact plate, that is, the included angle between the moving direction of the material impacting the impact plate and the vertical line of the impact plate. According to the collision theory, when the material collides with the impact plate along the vertical line of the impact plate surface, that is, the force is the largest when it collides directly, so the crushing effect is better and the lining plate is less worn, so it should be δ= 0°。
To ensure that when the rotor moves to different positions, the materials collide vertically with the counterattack plate. The curve of the counterattack plate should be an involute, but the involute is difficult to manufacture. Therefore, the counterattack plate is often replaced by broken line and arc. Therefore, for the non involute impact plate, in order to make the impact at different positions be positive, it is generally δ= 1~2°。
6 rotor speed
Rotor speed is one of the important working parameters of impact crusher. It plays a decisive role in the production capacity, product particle size and crushing ratio of the crusher.
The test shows that with the increase of rotor speed, its production capacity and crushing ratio increase significantly, and the product particle size changes in the direction of fine. However, with the increase of rotor speed and power consumption, the wear of plate hammer is also accelerated, and the requirements for the manufacturing accuracy of the machine are also improved.
For coarse crushing, the circumferential speed of rotor is v = 15m / S ~ 40m / s, and for fine crushing, v = 40m / S ~ 80m / s. After determining the circumferential linear speed of the rotor, the speed of the rotor is v = 60x1000v / (π d)
Where n is the rotor speed, R / min; D is the diameter of the rotor, mm.
7 productivity
The productivity of impact crusher is related to the rotational speed and geometric parameters of rotor.
Among the parameters of the impact crusher, the suspension position of the impact plate has the greatest impact on the performance of the crusher. After the equipment selection, other parameters have been determined. Only the suspension parameters of the reaction plate are adjustable. During production, they should be adjusted at any time according to the actual situation to adjust the machine to the best working state.
Rotor imbalance and serious wear of impact plate hammer are common disadvantages of impact crusher. Selecting appropriate plate hammer material and structure, necessary balance and balance correction are the key to solve the problem. During the operation of the equipment, correct operation and maintenance of the equipment, paying attention to the operation of the rotor at any time, and timely handling of problems found are also effective measures to improve the performance of the impact crusher.
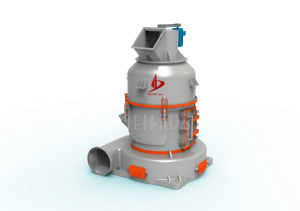