1.2 selection of grinding machine low-grade ore poses a dilemma for cartier mountain mine. In order to achieve economically satisfactory operation, large-scale production is required.
The rainwater is stored in the dam and enclosure + EI. In addition, the concentrator uses the grinding rainwater 9 and water for the concentrator according to the largest grinding machine designed and operated at that time. Dam 1 cofferdam stores the water I!. In addition, the mill is manufactured by SVEDALA Industrial Company, with a diameter of 12.2m (40 feet) and a power of 20MW. It is a gearless semi autogenous mill. This paper describes the details of the R & D, design, manufacture, installation and operation of the mill.
1 overview of Cartier Hill project 11 overview of concentrator Cartier hill mine is located 25km southwest of Orange City on the central plateau of New South Wales, Australia. The mine has rented about 31km2 of Cartier valley. The deposit is a large homogeneous low-grade porphyry gold copper deposit. The known reserves are 20.2 billion tons of ore, the gold grade is 0.73g/t, and the copper grade is 0.17%. The deposit contains 146.2t gold and 3.47 million tons of copper.
The mine includes open-pit mining and beneficiation, and the products are gold bars and gold copper concentrates. The raw ore processing capacity of the concentrator is 17 million T / A, with an annual output of 91000 t concentrate and 9.1 t gold. The concentrator works in two shifts every day, each shift is 12h, and the annual design operation rate is 94%. The concentrator consists of copper concentrator, water supply system, open-pit mine, tailings pipeline transportation and tailings dam, concentrate pipeline transportation and dehydration facilities located in Blayney (about 35km away from the concentrator).
The main equipment of the concentrator includes a coarse crusher, ore storage yard, a modified belt feeding system, Cartier semi autogenous mill (and 2) and two ball mills with a diameter of 6.7m. Some gold is recovered by gravity separation circuit, and the rest is recovered together with copper in flotation circuit of concentrator. After the concentrate is thickened, it is transported by pipeline to Blayney filter plant and railway loading station about 35km away. The tailings are pumped to the tailings dam, and the process water in the tailings dam is reused as recycled water.
The water supply system is designed to manage and collect part of the water in the local rivers, which is discharged and treated by Orange City, and a small part is treated by Blayney. The power is provided by 132kV overhead line in Orange City.
The selection of circuit configuration is that two 11. (diameter x length) semi autogenous mills are equipped with three 61mx 9.1m ball mills. However, this configuration cannot provide the most satisfactory economic scheme for the concentrator design project.
Two Svedala overflow ball mills with diameter of 6.1m and power of 8.6mw in the second section. The two mills are driven by two ring motors through speed reducers. The evaluation of one-to-one single series configuration shows that with the increase of mill specifications and the reduction of the number of mills, the total capital investment of the concentrator can be greatly reduced. However, increasing the mill size means that the Cartier mountain mine must use mills that have not been verified in design, i.e. 12.2mx 6.1m semi autogenous mill and 6.10.2m ball mill. Many people believe that this choice in the Cartier mountain feasibility study conducted by fluor Daniel davym is risky. Carry out risk analysis according to design risk, manufacturing risk, logistics risk, operation risk and maintenance risk. The risk analysis includes the evaluation of rotating structure, bearing and lubrication system, motor, driving device, power and control system, lining system, foundation system and auxiliary system (such as screening and feeding system).
The grinding test includes extensive cross-sections of a crack zone on the casting. To eliminate its defects, the blish National Design Association has been established 6. It will have a clear target in the purchase and production of equipment, which is the idea of both people and things. In most provisions, the technical specifications are required to be prepared by an editorial board composed of people with rich experience and many relevant data. For example, the gear design specification requirements are prepared by AGMA (American Gear Manufacturers Association). AWS is a specialized association on the responsibilities and obligations of engineers and inspectors, which is based on their respective scope of authority. However, only in the grinding equipment do we follow the processing technical requirements that can be described as “independent” without considering experience, experience and expertise.
Save money for the mine.
4 installation and commissioning due to thoughtful advance planning, the mill was installed smoothly. The main problem is related to the structural bolts of semi autogenous mill. These bolts are installed by ultrasonic length elongation measurement technology. When the length was initially checked, it was found that individual bolts were difficult to measure due to unstable signal. One of them was cut open and a discontinuous crack like line was found in the bolt cap.
Therefore, the bolt must be studied in more detail. Therefore, ultrasonic identification test is carried out for cracks. The crack was initially considered to be a temperature related forging problem when forging bolt caps. However, further analysis after mill assembly involves the problem of bolt rod material. The material is ordered by the bolt manufacturer and the brand is astm322. The peeling of bar seems to be a fundamental problem. Therefore, an identification method is being sought. The UT identification method of bolts is applicable to the effect of forging on peeling. However, this does not provide an identification method for bolt bars.
At the beginning of production, there were two problems involving large ball fracture and stator vibration. The hardness of the initial 125mm spherical medium is too high, so that many “hemispheres” are formed and leave the circuit through the lattice gap. This can be solved by the metallurgical process of the ball.
The motor stator starts to vibrate when the mill speed reaches about 9.7i/min. Initially, the stator structure was strengthened by adding support at the bottom of the stator to overcome vibration.
These supports eliminate unwanted vibration characteristics during mill operation. The essence of stator rigidity problem is further studied and finally solved. The mill specification is determined by the traditional method, that is, the driving power is scaled up according to the data of the Svedala database of the running mill. The diameter of the new mill is enlarged to the 25th power of the existing mill diameter. The effective length of the mill is directly amplified. The mill diameter used in these calculations is the inner diameter of the liner. This diameter is calculated from the average liner thickness assuming that the riser is “troweled”. The mill length is measured from the inner surface of the feed conical liner to the inner surface of the grid plate according to the traditional method. This value does not include the thickness of the riser at the feed end or discharge end.
If the riser is very large, the mill length value can be adjusted.
The drive power also depends on the mill feed composition. The test program provides ore bulk density for power calculation. The load density is calculated by ball load, rock load, slurry filling ball load gap and ore filling rock gap.
It is important to use the measured values obtained from semi industrial tests. The determination of these values shows that the most difficult ore blocks will accumulate in the mill. This cannot be reflected by the measured bulk density of certain types of ore transported by the mill feed belt. In some cases, when sampling from the ore in the mill, the ore accounting for up to 5% of the ore stones in the mill is taken as the representative composition of the mill load.
After the mill is put into operation, the actual driving power of the mill must be verified. It is the measurement result of 12 2m diameter mill in Cartier mountain mine operated at a given ore density and a given bulk density. The expected driving power value is very close to the measured value. The preferred method for determining the mill volume and ball volume is to use a measuring instrument fixed in the mill trunnion to carry out 5 groups of measurements, with 10 points in each group (50 points in total) to obtain the distance from the mill centerline to the load top surface. Other load measurement methods may be unreliable or produce wrong results.
5 when determining the power of the mill, it is important to determine the conditions of the mill liner and the changes in the internal dimensions of the mill.
This 4! The design exceeds the load rate change measured by asvedalac using a measuring instrument as shown in. It should be noted that the variation range of load level is about 0.75m, and the variation of load level at vertical height is shown as the power of Cartier mill measured under strictly controlled conditions. The relationship between mill power and speed obtained by the power distribution control system shows that the power required when the critical speed is 74% is close to the predicted driving power. In addition, when the speed increases to more than 74%, the power does not continue to increase as usually thought.
The ring motor is designed to have constant power at more than 74% of the critical speed. When a power pulse signal appears, it immediately follows the traditional and typical motor power limit. One view is that this control system can limit the motor current and prevent the motor from burning out.
The technical feature of the ring motor is that it has a constant torque at a certain design point (here 74% of the critical speed). Above this speed, the motor is designed as a constant power type.
Mill liner design is complex and requires deep understanding, especially on oversize mills. Using the mill trajectory program and load motion simulation device, as well as the research of raamani and valdeitama, the whole mill liner can be accurately designed.
Obviously, the liner design will affect the economy of the mill. Its design mainly affects the ball wear speed, liner wear speed, mill operation and Powell’s method. The inclined angle of the lifting plate will reduce the impact on the ball load, so as to reduce the crushing and consumption of the ball.
Svedala has conducted tests for many years and continues to study the improved liner design and its impact on driving power. The large semi autogenous mill can have 36 lifting plates per circle, 24 lifting plates per circle and 12 lifting plates per circle. Here, the setting of 24 lifting plates per circle is selected. If the number of lifting plates per circle is less than 24, the power required for effective and stable operation cannot be generated.
The riser design will affect the power curve. By increasing the angle of the leading edge of the riser, under certain load conditions (mill volume, percentage of ball load, percentage of solids, bulk density of solids expressed in percentage), the mill will need higher speed to achieve the expected power. The ring motor is flexible and can change the mill operation arbitrarily.
The variable speed drive with traditional ring gear and pinion structure must be strictly controlled because of its influence on the gear train. It is required to control the torque value of the gear train through speed, so as to control the motor driving power.
From the work done in Cartier mountain mine, it is obvious that the error between the predicted and actual measured power is within a reasonable range. The 12.2m semi autogenous mill can be designed and operated according to the current power data of large mill. It is an important work to accurately collect and process the operation data of large mill. At this time, it should be considered to determine the actual mill and load conditions, and measure the actual output power of mill motor.
6 liner characteristics 1 rubber discharge port the rubber protected pulp discharge port originally installed in this mill at Cartier mountain mine was worn out soon. The mill was replaced for the first time 12 months after it was put into operation. Many people believe that the reason is the premature failure of the discharge port. Some of them believe that the material “block” is captured at the outer circle of the discharge chamber and moves on it, and cannot be discharged at 80% of the critical speed.
The current design borrows the curved discharge port design used by unidirectional mill. It has some bends in the discharge chamber and forms a circular spoon at the end of the pulp lifter. The fully curved lifter design is not suitable for the Cartier mountain mine mill because it is bidirectional. Changing the operation mode to one-way is uneconomic and will greatly shorten the service life of the mill liner system.
6.2 roller screen plate and its development power 99svedala company has the above procedure and the characteristic of mcmlish failure is that the support line of the screen plate is disconnected. Initially, the rubber drum screen plate provided for the semi autogenous mill had problems in the early days of bookmark2 Cartier mountain mine. These problems are manifested in the failure of the sieve plate material, and it is required to replace the sieve plate regularly (generally 5 weeks). The sieve plate has been attributed to the impact of a large number of broken balls and large particle discharge products at the beginning of production.
Svedala tested several improved designs, including steel reinforced sieve plates (transverse and longitudinal reinforced sieve plates were tested), changing the rubber composition and canceling several sieve holes (increasing the hole spacing of installation bars). The current design adopts bite type combined sieve plate, which is made of special rubber to solve the problems of wear and strength. This design extends the service life of the drum screen plate from 5 weeks to 24 weeks.
7 step by step plan Cartier mountain mine is undertaking a concentrator optimization study to economically improve the processing capacity of the concentrator. Several improvements to the grinding circuit are being studied. Two of them are to increase the speed of the ball mill and expand the drum screen of the semi autogenous mill. Cartier mountain mine is considering increasing the speed of the ball mill to improve the grinding driving power and processing capacity. It is believed that this can improve the treatment capacity at similar grinding particle sizes. The main problem of mill speed increase is the increase of impact and wear with the increase of processing capacity.
Increasing the length of drum screen of semi autogenous mill is also related to increasing the processing capacity. The proposed changes include increasing the length of the drum screen by 1.6m to 68m. For such a length design, some problems are raised, including the additional load of the base and the drum screen itself. Therefore, the strength of journal liner, journal bearing load capacity, threaded connection design and roller screen design need to be considered. In industry, it takes 25A to accept a mill with a diameter of 11m to a mill with a diameter of 122m. This development has increased the mill capacity (compared with the maximum 11m diameter mill) by more than 30% and reduced the basic investment.
The work of Cartier mountain mine has proved that this large mill can be reliably designed, manufactured and operated, and the reliability of large mill can be predicted. In addition, the expected power and performance have been achieved. This large mill can also be used in other planned design projects of large concentrators, and they are confident of success.
(Wu Jianming, Linsen) (020905) (continued from page 39) in some concentrators abroad, harder ores were received due to the deepening of open-pit mines. Although measures such as re crushing of products with critical particle size and adding grinding balls were taken, it was still found that the production capacity of semi autogenous mills decreased sharply.
In many concentrators (such as ray concentrator in the United States, Kidston concentrator in Australia, mintek concentrator in South Africa and Codelco concentrator in Chile), a part of coarse crushed raw ore is pre crushed by standard crusher before semi autogenous grinding process to deal with this trend. This process method can ensure that the processing capacity of the mill can be increased by 30%. In some CIS countries, the most famous and largest example of semi self grinding process using domestic equipment is hobouck mining and metallurgy company.
In the design of some new large concentrators in Russia and some enterprises in CIS countries, the semi self grinding scheme has been adopted by the majority, such as udokan copper concentrator in Russia, choanhpbck concentrator in new Norilsk, oekibe concentrator in the Republic of Kazakhstan and aumimck in the Republic of Uzbekistan Copper concentrator of mining and metallurgy company. Unfortunately, most of these enterprises use imported mills.
Conclusion the current situation and Prospect Analysis of ore preparation technology and process before beneficiation show that the following new energy-saving and resource-saving processes must be further popularized: including coarse crushing in open stope, and then using trunk conveyor and large inclined belt
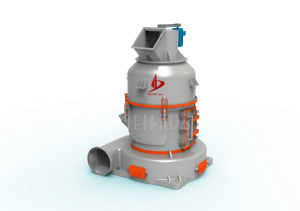