Raymond mill, also known as hanging roll disc mill, is a pulverizer imported from abroad.
1. Who invented Raymond mill?
In 1906, C.V. grueber established curt von grueber machinery manufacturing plant in the southern suburb of Berlin. Using his patent obtained in the United States, he produced the first maxecon mill, which was used in the moabit power station of bewag in Berlin as coal grinding equipment, with grinding energy up to 5t / h. nearly 600 units were sold in a few years and applied to the grinding fields of different industries. E. After C. Loesche became a shareholder and took charge of curt von grueber machinery manufacturing plant, he decided to purchase the Raymond centrifugal ring roller mill patent published in the United States and produced the first generation Raymond mill system.
However, since the grinding force (centrifugal force) of Raymond coal mill roller was limited by the roller diameter and speed at that time, the mill was only suitable for soft, low ash and good grindability coal materials at that time, while Germany’s coal was hard and high ash, requiring higher grinding force. Raymond coal mill with this structure was difficult to meet the grinding requirements, Therefore, Raymond coal mill has not been popularized in Germany. At that time, Raymond coal mill was just suitable for the grinding requirements of American coal, so Raymond coal mill was widely popularized and applied in the United States at that time.
2. Who improved Raymond mill?
In 1925, E.C. Loesche summarized the use characteristics and structural disadvantages of the first generation Raymond coal mill, decided to further improve the grinding structure of Raymond mill, and developed a mill with the opposite grinding principle, which is called improved Raymond mill. The ventilation of the improved Raymond mill system has two modes: positive pressure and negative pressure direct blowing. The Raymond Mill patent of this type was soon purchased by combustion engineering. Because the improved Raymond mill still has the problem of ring roller mill, although the roller diameter increases slightly, the grinding force increases little.
Later, Raymond branch of American combustion engineering company developed a new generation of Raymond mill, called VR mill. This Raymond mill is similar to the present leicher mill in many aspects. It should be noted that it is different from the conical grinding roller and flat grinding disc of leicher mill, and uses cylindrical grinding roller and grinding disc with inclined grinding surface with an angle of 15 degrees. During inspection and maintenance, the grinding roller has a roller turning out device similar to the leicher mill, and is also equipped with a protective device to prevent metal contact between the grinding roller and the grinding disc. In addition, the grinding roller can be lifted in advance before the mill is started, which can reduce the starting torque of the motor. Raymond mill is usually used to prepare pulverized coal in the industrial application in the United States. The fineness of the product varies between 250-325 mesh. It can adjust the fineness and output of the product during operation.
Since May 31, 1995, Raymond mill was the first to apply for a patent with its product name, it has been nearly 15 years. With years of development and improvement, there are more and more types and models of Raymond mill. Due to its stable performance, strong adaptability and high performance price ratio, Raymond mill has been introduced into China for many years and has been highly praised by the majority of users, It occupies a very important position in crushing equipment.
3. Working principle of Raymond Mill
The working principle of Raymond mill is as follows: the materials to be crushed are added into the machine from the feed hopper on the side of the hood. Relying on the grinding roller device suspended on the plum blossom frame of the main engine, it rotates around the vertical axis and rotates itself at the same time. Due to the centrifugal force during rotation, the grinding roller swings outward and presses tightly against the grinding ring, so that the shovel blade scoops up the materials and sends them between the grinding roller and the grinding ring, The purpose of crushing materials is achieved due to the rolling and rolling of the grinding roller.
At present, there are many domestic manufacturers of Raymond mill, such as Guilin Hengda Mining Machinery Co., Ltd. There are also many models, such as suspension roller Raymond mill, vertical Raymond mill, R-Raymond mill, etc. Raymond mill has outstanding advantages, strong applicability and high market share.
4. Application scope of Raymond Mill
Raymond mill is widely used in quartz, talc, marble, limestone, dolomite, lime, activated clay, activated carbon, bentonite, kaolin, cement, phosphate rock, gypsum, graphite, glass, manganese ore, titanium ore, copper ore, chrome ore, refractories, thermal insulation materials, clay, titanium dioxide, iron oxide, etc. the Mohs hardness is below 9.3, High fine powder processing of more than 300 kinds of materials in nonflammable and explosive mineral, construction, chemical, chemical fertilizer and other industries with humidity below 6%. The particle size of finished products is in the range of 60-325 mesh (0.125mm-0.044mm), and the maximum particle size of a small number of materials can reach 1000 mesh (0.013mm) as required.
5. Functional characteristics of Raymond Mill
Although different models of Raymond mills have their own advantages and different performance characteristics, General Raymond mills have the following characteristics:
(1) The whole Raymond mill is a vertical structure with relatively small floor area, strong systematicness and complete set. It can form an independent production system from the rough processing of raw materials, transportation, pulverization and final packaging.
(2) Compared with other grinding equipment, Raymond mill has high screening rate. The particle size screening rate of finished products ground by Raymond mill can reach more than 99%, which can not be achieved by other grinding equipment.
(3) Electromagnetic vibration feeder is adopted for uniform feeding, easy adjustment, small volume, light weight, oil and electricity saving and convenient maintenance.
The electric adopts centralized control and advanced type selection, which can realize unmanned operation in the host machine room.
(4) The transmission device of the main engine adopts a closed reducer, which has stable transmission, reliable operation and no oil leakage.
(5) The blade holder of the main engine is always in contact with materials during operation, so the blade holder is composed of upper and lower parts. After the lower seat is worn, remove the connecting bolts for replacement.
(6) The important parts of Raymond mill are made of high-quality castings and profiles. The fine process and rigorous process ensure the durability of the whole set of equipment.
6. Problems in Raymond Mill
With the extensive development of non-metallic minerals in the field of ultra-fine powder application in recent years, downstream enterprises have higher and higher requirements for non-metallic mineral products, especially for product fineness. Some problems existing in traditional Raymond mill have been perplexing mineral processing enterprises and equipment manufacturers. These problems are mainly reflected in:
(1) The product fineness is low, and the fineness of ordinary Raymond mill is generally below 500 mesh. These equipment can only occupy the low-end powder application market and can not adapt to the trend of fine development of China’s powder industry in the future.
(2) High mechanical failure rate, high power consumption, high noise and high emission pollution.
The system efficiency is low, the separation effect of the product collection system is not ideal, and a large amount of fine powder can not be effectively collected, resulting in repeated circulation in the system, resulting in power waste.
(3) There is a mistake in the design of the air duct of the main engine bellows. The larger particles in the materials entering the grinding area and the particles that can be ground and crushed in the future are often thrown into the bellows, gathered at the tail of the worm box and continuously extended forward, so that the excessive air volume is gradually reduced, which is easy to cause traffic jam, no powder or less powder, affecting the production.
In order to solve these problems and meet the needs of the market, many Raymond mill manufacturers have improved and innovated the traditional Raymond mill. Although these problems have been improved through the efforts of Chinese manufacturers and R & D personnel, the new Raymond Mill began to occupy the market. However, due to the different qualifications of various enterprises, new technologies cannot be applied in some enterprises with limited scale and weak R & D ability. Therefore, some problems still exist in China’s Raymond Mill Market to a certain extent. In fact, since the introduction of the first Raymond Mill in China, relevant enterprises have been committed to the improvement of Raymond mill. The technical improvement of Raymond Mill in China tends to be more efficient and practical, which is not only the necessity for Raymond mill to meet the needs of China’s market, but also the necessity for the development of Raymond mill industry.
7. Development trend of Raymond Mill
For a long time, the pulverizer industry in developed countries in North America and Europe has developed rapidly and is far ahead in the whole industry market. Its development speed is higher than the average development speed of the pulverizer industry, and its pulverizer industry is also relatively perfect. The milling equipment made in developed countries is becoming more and more sophisticated, and is developing towards the direction of higher and higher level of automatic control.
From the development of domestic milling industry, China’s milling equipment industry has developed very rapidly in recent years. At present, China’s milling machine manufacturing has been quite proficient, and the milling machine industry is booming. Moreover, the development trend of milling equipment industry will promote the development of all aspects of China’s milling industry in the future.
Specifically, China’s domestic grinding equipment has not only achieved simplicity, easy operation and easy maintenance in the production structure, but also paid more attention to the diversification of equipment performance, and the cost performance of grinding equipment has also been greatly improved. In addition to the continuous improvement of grinding equipment models, China has also greatly improved the control level of grinding machines. At the beginning of the 21st century, China’s pulverizers are still in a relatively backward state and backward in all aspects. In just a few years, the market of pulverizing equipment in China has been close to and has begun to catch up with and surpass the pulverizing equipment made in developed countries.
There have been two changes in the development of China’s domestic beneficiation equipment manufacturing industry. One is the transformation of product development from imitation to independent innovation; Second, the economic operation has changed from extensive type to benefit type. It is expected that the development trend of milling equipment industry in the future will be towards large-scale, digital intelligence and green energy saving.
With the continuous development of powder industry, the application requirements of Raymond mill are also improving. Raymond mill is the main grinding equipment in China’s powder industry. In order to meet the requirements of different application fields, it is an inevitable trend to develop to “high reliability, energy saving, precision and automation”.
(1) More energy saving and environmental protection
In recent years, all walks of life pay more and more attention to green environmental protection. With the proposal of the “green 12th Five Year Plan”, energy conservation and environmental protection has become a wind vane for the development of all industries, especially Raymond mill industry.
With the increasingly stringent requirements of green environmental protection, the State encourages the development and processing of mining industry and has high standards for mining machinery. The R & D and manufacturing of Raymond mill should pay more attention to the research on high efficiency and energy saving, and improve the manufacturing of key links such as zero pollution, high efficiency, low energy consumption and mechanical life. As far as Raymond Mill Market is concerned, energy-saving and environmental protection equipment with large processing capacity, high sorting efficiency and low energy consumption will be more favored, and the market demand will be more urgent.
(2) The automatic control system is more perfect
Raymond mill will mainly develop in the direction of high reliability, accuracy, automatic working condition monitoring and automatic control in the powder industry.
Measures such as thyristor power supply, AC frequency conversion speed regulation, centralized grease lubrication and shock absorption can be adopted, and devices such as working condition monitoring and microcomputer automatic control are provided. Among them, high reliability needs to enhance the wear resistance of grinding ring and lower gland through the rationalization research of mechanical principle, and improve the lubrication before each bearing of the machine under continuous working state.
Experts believe that automatic working condition monitoring and automatic control need to add a high-intelligent electronic control system inside Raymond mill to automatically control the incoming and outgoing of materials, grinding and quantitative control. Automatic control can effectively improve the working efficiency, accuracy and safety of Raymond mill. The operator only needs to press button control in the operation room.
(3) The grinding accuracy will be greatly improved
With the continuous improvement of the fineness requirements of powder products in the application field, the grinding equipment industry is bound to develop in the direction of refinement and scale, and Raymond mill is no exception.
For a long time, Raymond mill products have rarely made breakthrough improvements. Although the classification system has been greatly improved, it mostly stays in the transformation of single machine. As a manufacturer of production equipment, there are not many formal products. In many parameters, such as the size of grinding roller and grinding ring, host power and spindle speed, Raymond mill has few surpasses. In fact, Raymond mill has a lot of potential to be tapped.
To improve the grinding accuracy of materials, it is necessary to strengthen the accuracy of the analyzer. This problem has always been a technical difficulty in the improvement of Raymond mill, but it is also one of the main bottlenecks in the development of Raymond mill. Therefore, in the future, the grinding accuracy of Raymond mill will be the research and development focus of relevant enterprises and R & D personnel, which will also be the key to determine the future development of Raymond Mill in the mill industry.
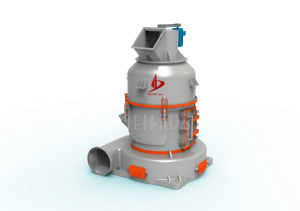