Under the current high pressure of environmental protection, many industries are facing severe tests, and enterprises also put environmental protection in an important position of enterprise development. Bag filter is an efficient dust removal equipment for air pollution control, which is widely used. Understand the common faults and solutions of bag filter, and can easily deal with emergencies. In the process of dust removal system operation, users pay more attention to the service life and work efficiency of dust collector, usually neglect the use of dust collector bag safety problems and routine maintenance. Do a good job in daily maintenance, timely troubleshooting, dust removal equipment can work more stable and efficient. The following are the routine parts of the bag filter to be checked and common faults and troubleshooting methods.
Conventional checkpoint of bag dust collector:
Air duct: Check for corrosion, leaks, or any external damage. Check whether there are bolts loose, welding cracks and ash accumulation in any parts (mainly flat pipe, reducer).
Solenoid/pulse valve: Check if it works correctly: listen to the sound of compressed air blowing.
Pressure reducing valve: whether leakage. Notice that there are sundries inside the pressure reducing valve
Fan: Ensure that the fan is firmly installed and level, regular refueling. Note that dust tends to accumulate on the blades.
Compressed air system: Check whether the compressor is correctly filled with lubricating oil. Check whether there are cracks on the air pack and pipeline; Note the pressure indication of the regulating valve (if installed). Check whether the air compressor and air bag release water.
Access door: All access doors should be tightly sealed. Check whether the sealing strip is loose, cracked, or worn. Replace as needed.
Inlet/guide plate: Check for excessive wear or corrosion.
Air volume regulator and lift valve: check whether the oiler (if required) is operating properly.
Common faults and troubleshooting methods of bag filter
1. High pressure difference of dust collector
Main reasons and elimination methods:
Differential pressure reading error: clean pressure gauge interface/check gas pipe for cracks/check differential pressure gauge.
Incorrect setting of blowing system: increased blowing frequency/compressed air pressure is too low; Increase pressure/check dryer, clean (if necessary)/check for blockage in line.
Injection valve failure: check diaphragm valve/control solenoid valve.
Pulse controller failure: check whether the controller indicates each contact/check the output of each terminal.
Filter bag blockage: condensation on the filter bag (see below); The filter bag was sent to the laboratory for analysis. Filter bag drying and deashing treatment/or change/reduce air volume/increase compressed air pressure/add deashing frequency/spray neutral powder to form a protective layer and porous primary cake.
Excessive secondary dust: continuous ash hopper/each filter bag/cartridge is cleaned in a random sequence rather than in sequence. Check inlet baffle plate to make sure it is clean.
2 Fan motor current is low/air volume is low
Main reasons and elimination methods:
High pressure difference of dust collector: see above.
Reverse connection of fan and motor pulley: check the drawing and reverse connection of pulley.
Pipe ash blockage: clean the pipe, check the gas flow rate.
Fan baffle closed: open baffle and lock in the open position.
Dust collector lift valve close: check the air path, open the valve plate.
System static pressure is too high: measure the static pressure at both ends of the fan and check the design specifications, adjust as required. For high flow rate check pipe to replace the original bad design.
Fan not operating within design requirements: check fan inlet structure to ensure smooth airflow. Check blade for wear and repair or replace as needed.
Reverse rotation of the fan: reverse connection of the motor.
3 Dust escapes from the collection point
Main reasons and elimination methods:
Low air volume: see above.
Pipe leaks: Repair cracks so that dust does not bypass dust collection points.
Pipeline balance is not correct: adjust branch pipe damper.
Unreasonable design of suction hood: close the open area around the dust collection point. Check whether the flat suction ventilator overcomes suction. Check whether the dust is taken out of the hood by the belt.
4 The chimney belches out ashes
Main reasons and elimination methods:
Filter bag leakage: replace if the filter bag is torn or has a small hole. Check spring coil installation to ensure tight.
Plate leakage: fill gap or weld.
No enough dust cake: reduce the pressure of compressed air; Reduce cleaning frequency/spray neutral powder to produce primary dust cake.
Filter bag or cartridge with too many holes: filter bag or cartridge for permeability test, and consult manufacturer.
5 The fan is severely worn
Main reasons and elimination methods:
Fan treatment of excessive dust: see above.
Improper fan: determine whether the fan is suitable for working conditions; Consult manufacturers.
High fan speed: consult the manufacturer.
6 The fan vibrates severely
Main reasons and elimination methods:
Dust accumulation on wheel blades: clean the dust on wheel blades and check whether the fan handles excessive dust. Check the fan installation position, drain condensate or moisture, or keep the fan dry.
Fan impeller is not suitable for working conditions: consult the manufacturer.
Belt pulley unbalance: belt rotation power balance.
Bearing wear: replacement.
7 The compressed air usage is too high
Main reasons and elimination methods:
Overfrequency of cleaning cycle: Delay the cleaning cycle (if possible).
Too long spraying time: reduce the duration (except after the initial impact, all the other air is wasted; Usually the spray is set to 0.1 seconds).
High pressure: check diaphragm and spring (see analysis of valve failure).
Trachea leakage: bubble test and repair.
8 The compressed air pressure is low
Main reasons and elimination methods:
High compressed air consumption: see above.
Tracheal resistance: Check whether the tracheal is blocked.
The dryer is blocked: replace the desiccant or bypass the dryer if the working condition permits.
Compressor wear: Consult the manufacturer or check the compressor maintenance manual.
9 The air volume is too high
Main reasons and elimination methods:
Pipe leakage: plug the crack.
Insufficient static pressure: close the air valve. Reduce the fan speed.
10 Low compressed air usage
Main reasons and elimination methods:
Pulse valve not working: check pulse valve as described above.
Controller failure: Check terminal output as described above.
11 Filter bag premature failure – decomposition
Main reasons and elimination methods:
Filter material is not suitable for this condition: analyze the chemical properties of the gas and consult the filter bag or cartridge manufacturer.
Filter material is not suitable for gas composition: in the dust collector before processing gas; Or replace the filter bag or cartridge.
Operating at acid dew point temperature: increase gas temperature.
High filter bag failure rate – excessive wear
Main reasons and elimination methods:
Uniform flow diversion baffle wear out: replace the uniform flow baffle.
Too much dust: install a primary dust collector.
Overfrequency of cleaning cycle: prolong the cycle time.
Inlet air flow not properly equalized by filter bag or cartridge: consult manufacturer.
Dust in the cleaning room/flower board: clean flower board and filter bag or filter cylinder inside; Fluorescent test to find the leak.
Burr/corrosion on cage frame (if used) : remove smooth burr; Replace as required. If corrosion, consider using corrosion – resistant coating cage frame.
13 Filter bag high failure rate – combustion
Main reasons and elimination methods:
Stratified distribution of hot and cold gases: Baffles are used in pipelines to solve turbulence.
Spark into dust collector: install spark eliminator.
Thermocouple failure: replace and find out the cause of failure.
Cooling unit failure: check design specifications, consult manufacturer.
Moisture in dust collector
Main reasons and elimination methods:
Insufficient heating: Input hot air into the system before beginning to process airflow.
No cleaning system after shutdown: run the fan for 15~20 minutes after the system is shut down.
Shell temperature lower than dew point temperature: raise gas temperature/unit insulation insulation/reduce moisture in the system to reduce dew point temperature.
External air into the dust collector: check whether the shell leakage, door seal wear.
Insulation layer with cold objects: eliminate direct metal lining.
Vapor in compressed air: Check automatic drainer/install secondary cooler or dryer.
The process condition becomes worse: spray the modulation powder.
15 Bridge material in ash hopper
Main reasons and elimination methods:
Moisture in dust collector: see above.
Ash hopper design prevents material movement: install sound horn or vibrator to facilitate material movement.
Dust accumulation in the ash hopper: continuous ash discharge; Do not ash in the ash bucket memory.
Conveyor opening is too small: the use of wide flaring groove blade; Feeder/star discharge valve not functioning or undersized.
The above are some fault phenomena which are easy to appear in the operation of bag filter. Do a good job of daily maintenance, timely find and solve the hidden trouble, ensure the stable operation of dust collector, can effectively improve the efficiency of dust removal. The storm of environmental protection is back, has your enterprise done a good job of environmental protection measures?
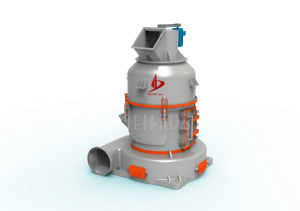